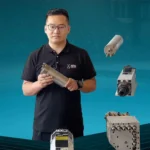
Fix Edge Chipping in Panel Furniture Cutting: Causes & Solutions
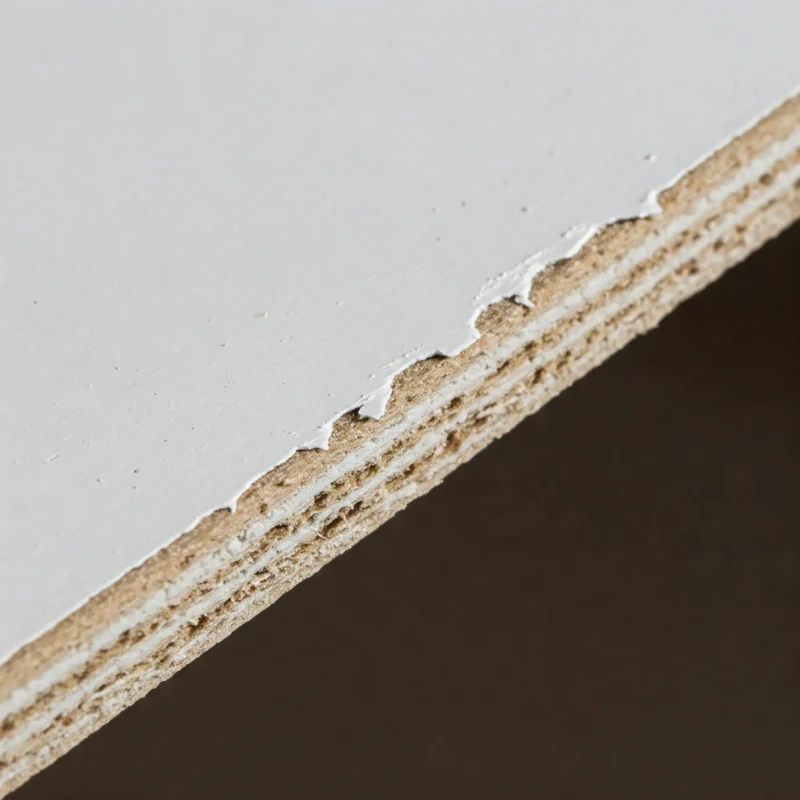
What Causes Edge Chipping in Panel Furniture Cutting?
Edge chipping, sometimes called tear-out or collapse, happens when the edges of a panel splinter or break during the cutting process. It’s particularly prevalent with materials common in panel furniture, such as MDF, particleboard, and laminated boards. Understanding the main culprits is the first step to solving the problem:
1. Material Quality and Properties
Panel furniture often utilizes boards like MDF or particleboard covered with a decorative layer, such as melamine. While cost-effective and visually appealing, these surface layers can be hard yet brittle, lacking the toughness to resist chipping under cutting stress. Low-density or lower-quality core boards are especially vulnerable due to weaker structural integrity.
2. Dull or Inappropriate Cutting Tools
A dull blade or router bit is a primary cause of tear-out. Instead of slicing cleanly, it rips through the material, leaving ragged edges. Using the wrong tool for the job – for instance, a blade with too few teeth (low TPI) or incorrect tooth geometry for laminates – exacerbates the issue. A blade designed for solid wood might struggle with the layered structure of particleboard.
3. Improper Feed Rate and Spindle Speed
The balance between the feed rate (how fast the material moves) and the spindle speed (how fast the tool spins) is critical. Too fast a feed rate overloads the blade, causing chipping. Too slow, and friction can generate excessive heat, potentially burning the material or dulling the tool faster, leading indirectly to poor cut quality. An incorrectly matched spindle speed also contributes to uneven cutting forces.
4. Tool Eccentricity and Installation Issues
If the cutting tool isn’t installed correctly and securely in the collet, it can become unstable. Improper clamping can lead to tool eccentricity (wobble or vibration). This instability directly impacts cut precision and increases the likelihood of chipping. Dust or debris buildup in the clamping nut or collet can also compromise a secure fit, emphasizing the need for regular cleaning during tool changes.
5. Insufficient Panel Support and Vacuum Table Performance
Panels need to be held rigidly during cutting. Vibration or movement allows the material to shift against the blade, causing uneven pressure and chipping. Many CNC routers use vacuum tables to secure panels. However, if the vacuum suction is weak (often due to poor pump performance or leaks), the panel, may not be held firmly enough, leading to poor cuts.
6. Incorrect Blade Height or Cutting Depth
Setting a circular saw blade too high above the material increases the aggressiveness of the cut, potentially causing upward tear-out on the top surface. For CNC routers, cutting too deep in a single pass puts excessive stress on the material and the tool, particularly problematic with double-sided laminates.
Real-World Example: Solving Edge Chipping with HALOONG CNC
Consider a furniture workshop experiencing significant edge chipping (around 25%) on their melamine cabinets produced with a standard CNC router. Investigation revealed a combination of a dull bit, an overly aggressive feed rate, and inadequate workpiece holding due to a subpar vacuum table. By upgrading to a HALOONG CNC cutting machine known for its robust vacuum system and precise controls, and pairing it with a recommended high-quality carbide bit, they drastically reduced chipping to less than 5%. This not only saved material but significantly improved product quality and customer satisfaction.
How to Prevent Edge Chipping: Practical Solutions
Armed with the knowledge of the causes, let’s dive into effective solutions. Implementing these tips, potentially alongside equipment upgrades from HALOONG CNC, will help you achieve consistently clean cuts.
1. Select Quality Materials
Start with the source. Opt for boards with sufficient density and a durable laminate surface that can better withstand cutting forces. While potentially slightly more expensive initially, higher-quality MDF or particleboard reduces waste and rework, saving money long-term. Pro Tip: Always test cut a sample from a new batch before full production.
2. Use High-Quality, Sharp Tools Designed for the Material
Invest in the right cutting tools and keep them sharp. For laminates like melamine, a high-tooth-count (e.g., 80-100 TPI for a 10-inch blade) carbide-tipped blade with an appropriate grind (like TCG – Triple Chip Grind) is ideal. For CNC routers, consider compression spiral bits, which apply downward pressure on the top surface and upward pressure on the bottom, minimizing chipping on both sides.
Maintenance Tip: Inspect tools regularly. Replace or sharpen dull blades/bits immediately – a sharp tool is crucial for preventing edge chipping.
3. Optimize Feed Rate and Spindle Speed
Finding the sweet spot requires testing. Start with recommended settings for your material (e.g., for MDF, try ~18,000 RPM spindle speed and a moderate feed rate like 10-15 meters/min, adjusting based on results). HALOONG CNC machines offer precise control to fine-tune these parameters. If you see burning, consider increasing feed rate slightly or decreasing spindle speed. If chipping occurs, try reducing feed rate or ensuring optimal RPMs. Always test on scrap material first!
4. Ensure Proper Tool Installation and Maintenance
Cleanliness is key. Before installing a tool, ensure the collet, nut, and tool holder are free from dust and debris. A clean connection ensures concentricity and stability. Follow manufacturer guidelines for proper tool clamping torque. Check out HALOONG CNC’s maintenance guides for best practices.
5. Improve Material Support and Vacuum Performance
Ensure the panel is fully supported and cannot vibrate. Using a sacrificial backer board (like a thin sheet of MDF) underneath your workpiece provides support to the bottom edge, reducing tear-out. On CNC routers, maximize your vacuum table’s holding power by ensuring seals are intact, the spoilboard is surfaced correctly, and unused areas are covered. If your current machine struggles, consider the superior vacuum performance of HALOONG CNC models.
6. Utilize a Scoring Blade for Double-Sided Panels
For panel saws cutting double-sided laminates, a scoring blade is highly effective. This smaller blade makes a shallow pre-cut on the underside of the panel just before the main blade cuts through, preventing chipping on the bottom surface. Many HALOONG CNC panel saws offer this feature.
7. Adjust Blade Height and Cutting Depth Strategy
On table saws, set the blade height so the teeth just clear the top surface of the material (around 1/8 inch or 3-4mm protrusion is often sufficient). For CNC routers, avoid cutting the full depth in one go, especially with thicker panels. Use a multi-pass strategy, cutting in shallower increments (e.g., 1/3 or 1/2 the material thickness per pass). HALOONG CNC’s controllers make programming multi-pass cuts easy.
Advanced Tips for Flawless Cuts
If basic adjustments aren’t enough, consider these:
- Zero-Clearance Insert (Table Saws): This insert minimizes the gap around the blade, providing maximum support to the material right at the cut line, reducing underside tear-out.
- Equipment Upgrade: Persistent issues might indicate limitations of your current machinery. Investing in a robust HALOONG CNC machine with features like advanced vibration control, powerful vacuum, and precise motion systems can be a game-changer for cut quality and overall efficiency.
Why Clean Cuts Matter for Your Woodworking Business
Preventing edge chipping goes beyond aesthetics. It directly impacts your bottom line through:
- Reduced Material Waste: Fewer rejected parts mean lower material costs.
- Minimized Rework: Less time spent fixing errors increases productivity.
- Higher Quality Products: Flawless edges contribute to a professional finish, enhancing customer satisfaction.
- Improved Reputation: Consistent quality builds trust and encourages repeat business and referrals in a competitive market.
Investing in techniques and equipment like those from HALOONG CNC to achieve clean cuts is an investment in your business’s long-term success.
Take Control of Your Cutting Quality Today
Ready to eliminate frustrating edge chipping? Review your current process: assess tool sharpness, optimize cutting parameters, ensure solid workpiece holding, and maintain your equipment diligently. For a significant leap in performance and reliability, explore the range of CNC engraving and cutting solutions offered by HALOONG CNC. Their machines are engineered to deliver the precision needed for perfect panel processing.
Contact their experts to discuss how HALOONG CNC can help you achieve flawless cuts every time!
Frequently Asked Questions (FAQs)
Q: What’s the best blade/bit for cutting melamine without chipping?
A: For table/panel saws, a high-tooth count (80+ TPI) carbide blade with a Triple Chip Grind (TCG) or High Alternate Top Bevel (Hi-ATB) is recommended. For CNC routers, use sharp carbide compression or low-helix down-spiral bits. HALOONG CNC can advise on specific tooling.
Q: How can I prevent edge chipping on a budget without new equipment?
A: Focus on the basics: ensure your current blade/bit is extremely sharp. Optimize feed/speed settings through testing. Clean your tool clamping system thoroughly. Use a backer board. Apply masking tape along the cut line (can help sometimes, but is time-consuming).
Q: How often should I replace my CNC router bits?
A: This depends heavily on the material cut, bit quality, and usage intensity. Monitor cut quality closely. As soon as you notice even slight degradation (increased chipping, rougher edge), it’s time to replace the bit. Using durable bits, like those recommended by HALOONG CNC, can extend replacement intervals.
Q: What indicates a good vacuum table on a CNC machine?
A: Look for strong, consistent suction across the entire table, often achieved through powerful pumps and efficient zone management. Build quality, a well-surfaced spoilboard, and good sealing capabilities are crucial. High-quality machines like those from HALOONG CNC prioritize robust vacuum systems for reliable workpiece holding.
Q:There is no solutions about edge banding machine chipping in this page. Where can I get help?
A:You can check out this blog specifically for edge chipping.Of course,you can contact us to get almost all service on furniture processing,
By systematically addressing the causes of edge chipping and implementing these solutions, you can significantly enhance your cutting quality, efficiency, and the overall standard of your furniture products. Still have questions? Reach out – we’re here to help!
Related Products
HALOONG CNC Cylindrical Shaft Polishing Machine
Dual Station Table Linear ATC CNC Wood Router: Automatic Tool Changer Wood CNC for Furniture Making
Why the HALOONG 12-Tool ATC CNC Wood Router Stands Out
The HALOONG 12-Tool ATC CNC Wood Router is a high-performance wood CNC machine built for exceptional efficiency and flexibility. Its automatic tool changer (ATC) switches between 12 tools in under 5 seconds, drastically reducing downtime and boosting output. Whether you’re cutting MDF, carving solid wood, or crafting intricate designs, this CNC wood router handles it all with ease. For even greater productivity, consider our optional dual-table configuration, which allows for near-continuous operation and significantly increases throughput for demanding production schedules.
Key Features of This CNC Wood Router
Here’s what makes this wood CNC a must-have:
Ultra-Fast Tool Switching
- 12-tool linear magazine: Holds a variety of tools, ready for instant use.
- Tool changes in under 5 seconds: The gantry-integrated design cuts travel time, keeping your production moving.
Versatile Material Processing
- Works with MDF, solid wood, OSB, PVC, acrylic, aluminum, and composite panels.
- Supports standard furniture joints (e.g., dowels and cams) and modern invisible connectors (e.g., Lamello, Peanut, Lockdowel).
- Perfect for cabinets, wardrobes, doors, and artistic carvings.
Customizable Worktable Options
- Options like 4'x8' (1220x2440 mm), 4'x9' (1220x2800 mm), or custom sizes available for single-table models.
- Maximize your output with our optional dual-table configuration, allowing for continuous loading and unloading on separate work zones.
- Upgraded vacuum table locks materials securely for flawless results on both single and dual-table setups.
Effortless Operation
- User-friendly controls with a clear display, network, and USB connectivity.
- Simplified design means even beginners can master it quickly. The dual-table operation is also intuitively managed through the advanced control system.
Built to Last with Precision
- Heavy-duty steel frame and high-precision gearbox for durability.
- Servo-driven system ensures smooth, accurate cuts every time. The robust construction ensures stability even during continuous operation on the dual-table model.
Cleaner, Safer Workspace
- Integrated dust collection and air-blow system keeps debris in check.
- Ideal for continuous, high-output runs without mess, making it perfect for the increased production demands of the dual-table system.
Top-Notch Support
- Free technical support, lifetime service, and remote assistance included.
PUR Glue Machine Kit For Edge Bander
Four-Spindle Dual-Station CNC Wood Router for Panel Furniture Manufactured
Maximize your panel furniture manufacturing throughput with the HALOONG Four-Spindle Dual-Station CNC Router. Expanding on the reliability of our single-station four-spindle CNC wood cutting machines, this dual-station system provides a substantial increase in production efficiency. It's designed for continuous operation, minimizing downtime and maximizing output through its smart workflow.
The clever dual-station workbench facilitates seamless alternating work cycles. While one station is engaged in machining, the operator can efficiently prepare the next batch of materials on the adjacent station. Upon completion of the first cycle, the machine instantly transitions to the pre-loaded second station. This continuous processing approach ensures no wasted time, making it a key asset for high-volume furniture production.